Geschweißte Zylinder bestehen aus Komponenten, die so optimiert sind, dass das auf dem Markt verfügbare Rohmaterial – hauptsächlich Rohre, Vollmaterial und Bleche, die in geeigneter geschweißt sind, damit der Zylinder die Anforderungen an Leichtigkeit, Kosteneffizienz und Marktverfügbarkeit erfüllt – bestmöglich genutzt wird.
Was die recht einfach gehaltene Ausführung betrifft, so ist zu beachten, dass diese Zylinder eine sorgfältige Planung und eine fachgerechte Ausführung der Schweißarbeiten erfordern. Ziel ist es, eine funktionale Schweißarbeit durchzuführen, die die Dichtigkeit unter Druck gewährleistet und keine Defekte an der Innenseite aufweist, die im Laufe der Zeit zu Schäden führen könnten.
Verwaltung der Schweißnähte
Die Schweißnähte können einen oder mehrere Stellen des Rohrs betreffen, wobei das Ganze natürlich die Zylinderlaufbuchse bildet. Das Schweißen in Rohren wird jedoch, wenn es nicht ordnungsgemäß im Rahmen einer vorausschauenden Konstruktion berücksichtigt wird, unweigerlich Ursache einer erkennbaren Verformung in den Rohren, da der Kolben während der linearen Bewegung einfach stecken bleibt, wodurch die Dichtung beschädigt und ihre Funktion beeinträchtigt wird.
Um dieses Problem zu beheben, sieht unsere Programmierung während des Produktionszyklus der Komponente einen Honvorgang im Anschluss an das Schweißen vor, um die oben erwähnte Verformung „auszugleichen“ und die gewünschte Geometrie wiederherzustellen, die ein optimales Gleiten des Kolbens in der Laufbuchse gewährleistet.
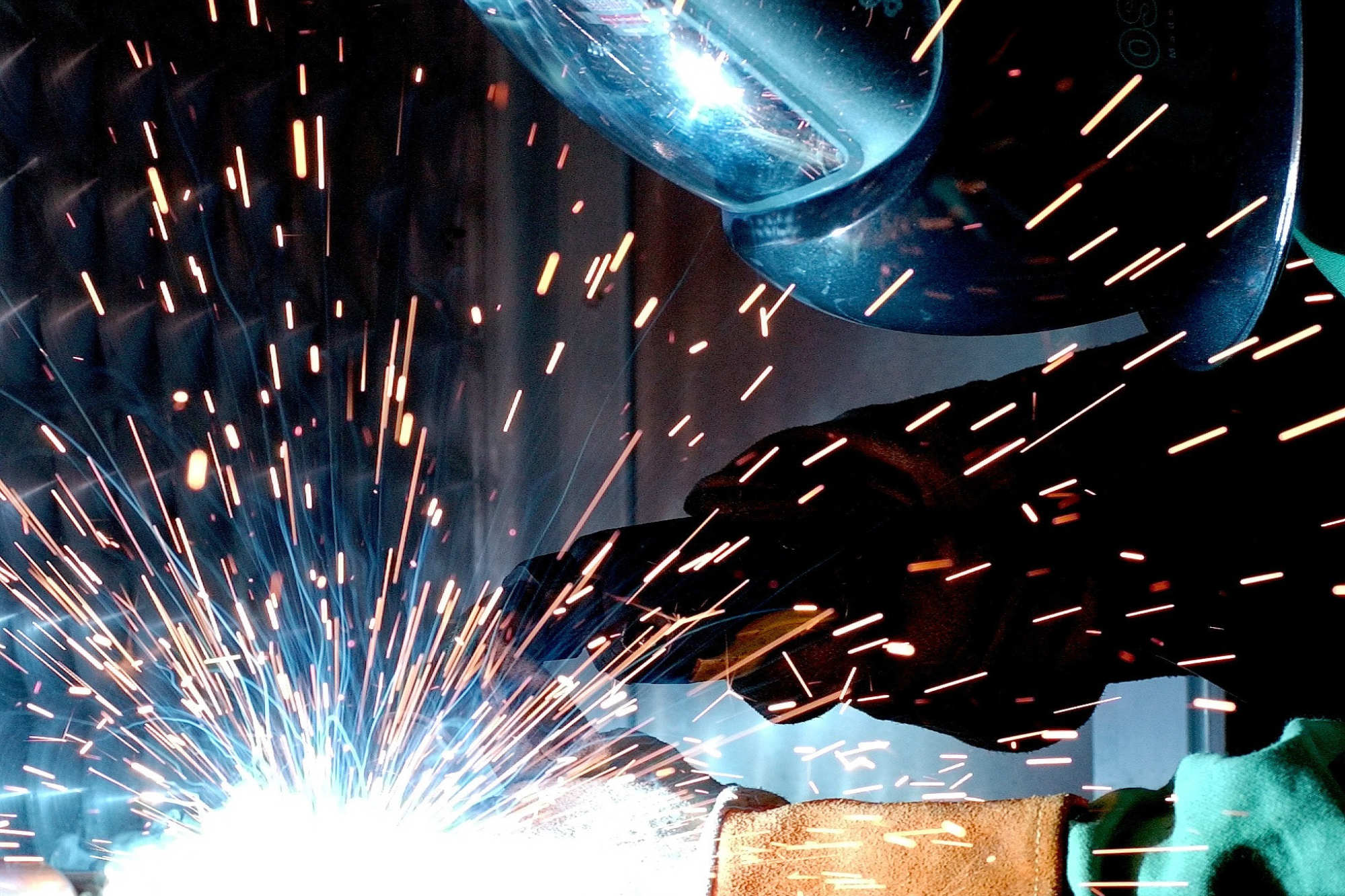
Mit Liebe zum Detail für beste Qualität
Dies gilt auch für unsere Produktion von kundenspezifischen und maßgeschneiderten Zylindern mit den Besonderheiten, die die verschiedenen Fälle auszeichnen. So müssen z. B. manchmal Schweißnähte angebracht werden, um die Stahlteile zu verbinden, in diesem Fall Öleinlassstutzen oder Zapfenhalterungen mit Stiften, und die Sorgfalt, mit der dies geschieht, hat einen großen Einfluss auf die Leistung des Systems.
In unserem Produktionszyklus
In unserem Produktionszyklus muss die Schweißnaht oft maschinell nachbearbeitet oder sogar verchromt werden, sodass es immer und in jeder Phase notwendig ist, jeden einzelnen Schritt bis ins kleinste Detail zu pflegen.
Nach einer sorgfältigen Planung der zu schweißenden Teile wird der Stemmmeißel nach den betriebseigenen Verfahren, mit der Bezeichnung WPS (Welding Procedures Specification), hergestellt. Geschweißt wird mit MIG 135-136, SG3 Schweißdraht, mit besseren Eigenschaften als dem Grundmetall, mit mehreren Durchgängen, bei denen jede Naht sorgfältig gebürstet wird, um mögliche Defekte an der Innenseite zu beseitigen.
Neben der sorgfältigen Vorbereitung und Reinigung der zu schweißenden Werkstücke wird während des Verfahrens die in Ampere gemessene Stromstärke überwacht, um ein vollständiges Eindringen der Schweißnaht in die Grundwerkstoffe sicherzustellen.
Auch die anfängliche Vorwärmung und das Abdecken der Werkstücke am Ende der Bearbeitung werden überwacht, um den thermischen Schock, der Veränderungen im Korn des Grundstahls verursachen könnte, so weit wie möglich zu begrenzen.
Am Ende des Zyklus wird die Schweißnaht mit Formschablonen auf ihre Maße überprüft. Auf Wunsch kann eine Magnetoskopie mit Ausstellung eines Berichts durchgeführt werden.
Bei der Prüfung des montierten Zylinders kann die Schweißnaht auch mit Luft geprüft werden, indem eine Detektorflüssigkeit verwendet wird, die, wenn sie auf die zu prüfende Stelle gesprüht wird, eventuelle Leckagen durch Auftreten von Blasen aufzeigt.
Der nächste Test wird mit Hydrauliköl mit einer Viskosität von maximal 32 cSt durchgeführt.